In 2010, our company decided to venture into robotic submerged arc welding (SAW). By creating robotic solutions, we have achieved significant improvements in welding quality and productivity. Our solutions can be used in various industries where multi-pass welding of annular, saddle, longitudinal and complex welds is required. We are able to increase productivity by 15-20% by optimising welding modes and improve weld quality, eliminate weld defects such as:
- Unwelded weld root;
- Hot cracks;
- Shrinkage cracks;
- Surface pores;
- Internal pores;
- Slag inclusions;
- Undercuts;
- Non-fusion.
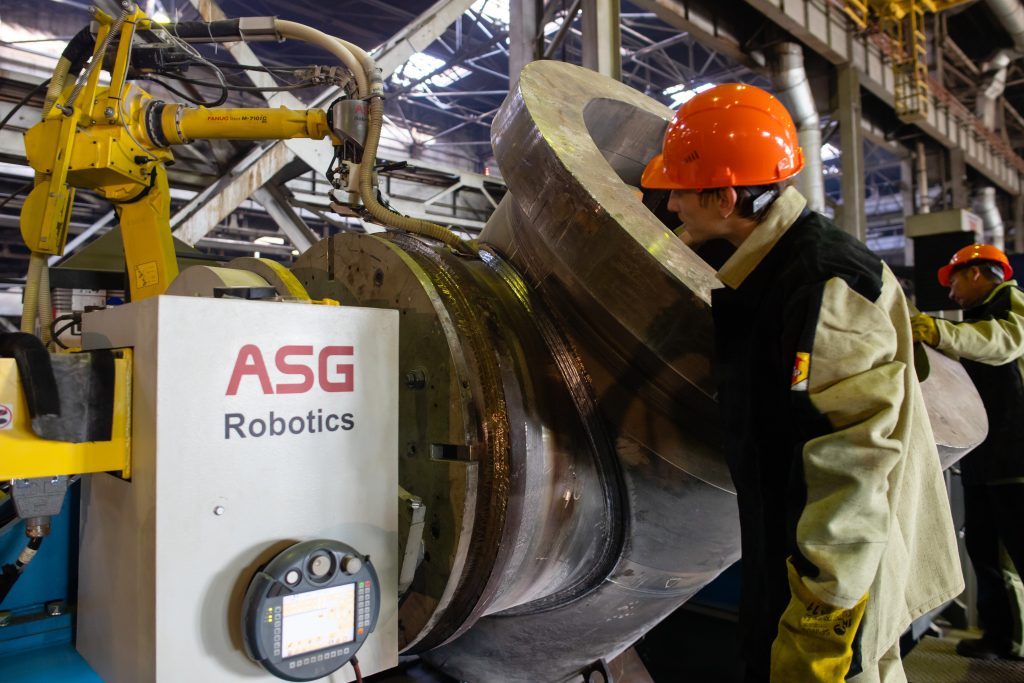
Submerged arc welding (SAW) is a versatile and widely used welding technology that has a number of pros:
1. High Productivity
Submerged Arc Welding is renowned for its high deposition rates, making it one of the most productive welding processes. The continuous and automated nature of SAW allows for rapid welding of thick materials, increasing efficiency and reducing labor costs.
2. Deep Weld Penetration
The technique excels in providing deep weld penetration, especially in thick materials. The depth achieved is influenced by the specific characteristics of the chosen welding electrode. This characteristic makes it suitable for welding heavy-duty structures, such as shipbuilding, bridges, and pressure vessels.
3. Minimal Fumes and Sparks
Submerged Arc Welding operates with a granular flux that covers the welding arc, minimizing exposure to the surrounding air. Consequently, the emission of fumes and sparks is significantly reduced, contributing to a safer working environment.
4. Мaterials Versatility
This method can be used to weld a wide range of materials (stainless steels, carbon steels, nickel-based alloys). This allows it to be used in various industries from manufacturing to construction.
5. Low Heat Input
The process generates low heat input compared to other welding methods, reducing the likelihood of distortion and minimizing the need for extensive preheating.
However, it also has its cons.
1. Limited Joint Availability
One of the major disadvantages of submerged arc welding is its limited accessibility to certain joint configurations. Its suitability is often limited to flat or horizontal welding positions, making it less versatile than some other welding processes.
2. Lack of Portability
The equipment used in SAW welding is often large and stationary, which limits its mobility. This lack of mobility can be a disadvantage in situations where welding or repairs are required on-site.
3. Equipment and Setup Costs
Submerged Arc Welding requires specialized equipment, including a flux recovery system.
By robotizing SAW welding, we were able to eliminate or significantly reduce its inherent disadvantages.
1. Limited Joint Availability
We have developed several types of welding heads, which makes the welding process widely versatile.
We have developed a robotic welding head: ASG Robotics WH-1
– with vertical flux feed (the welding head can deviate from the vertical position plus or minus 25°)
– for welding in a narrow gap
– with horizontal flux feed (welding head can deviate from horizontal position plus or minus 25°)
– for welding in hard-to-reach places ASG Robotics WH-2
If necessary, we develop special welding heads for a specific task.
2. Portability
We have developed a mobile Robotic cell MWC-01
The welding cell is made in a modular design. The cell includes everything necessary for SAW welding.
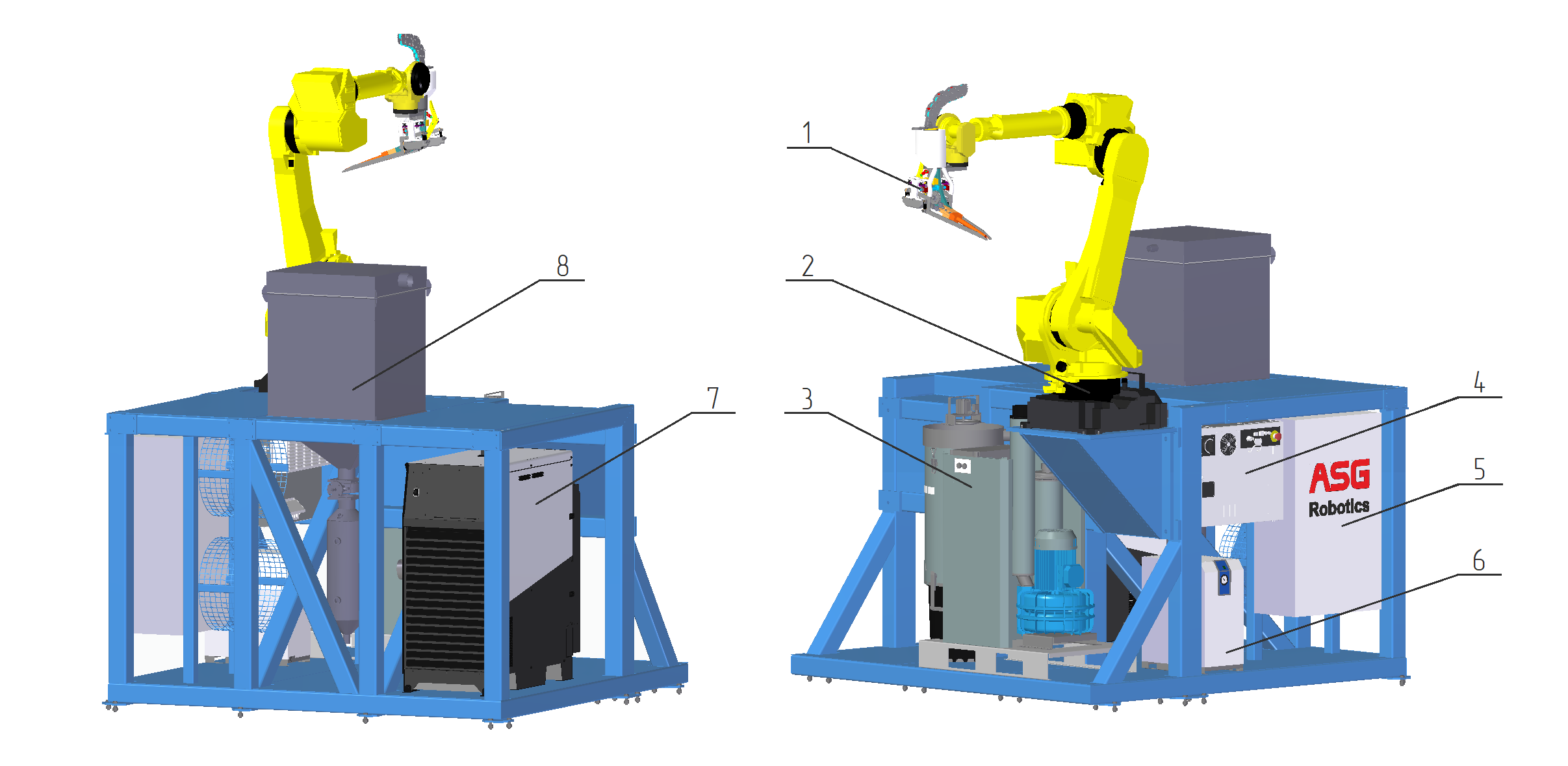
1 – Welding head ASG Robotics WH -1, ASG Robotics WH -2 or other special welding heads
2 – FANUC M-710iC robot mounted on a replaceable cell frame console
3 – Flux recirculation system based on Vacuum unit nederman L-PAK 150
4 – Robot controller
5 – Control cabinet
6 – AIR DRAYER SMC IDFA6E-23
7 – Welding machine POWER WAVE 1000AC/DC SD
8 – Flux tank
The module is compact and can be easily integrated into various welding systems.
It can be mounted in both right and left versions.
Transport position
The total weight of the platform is 2500 kg.
The cell can be moved using a forklift or crane, transported in 20-foot containers
By increasing the podium (p) and frame console (c), various combinations can be created for welding large-sized objects.
The podium and console are also made in a modular design
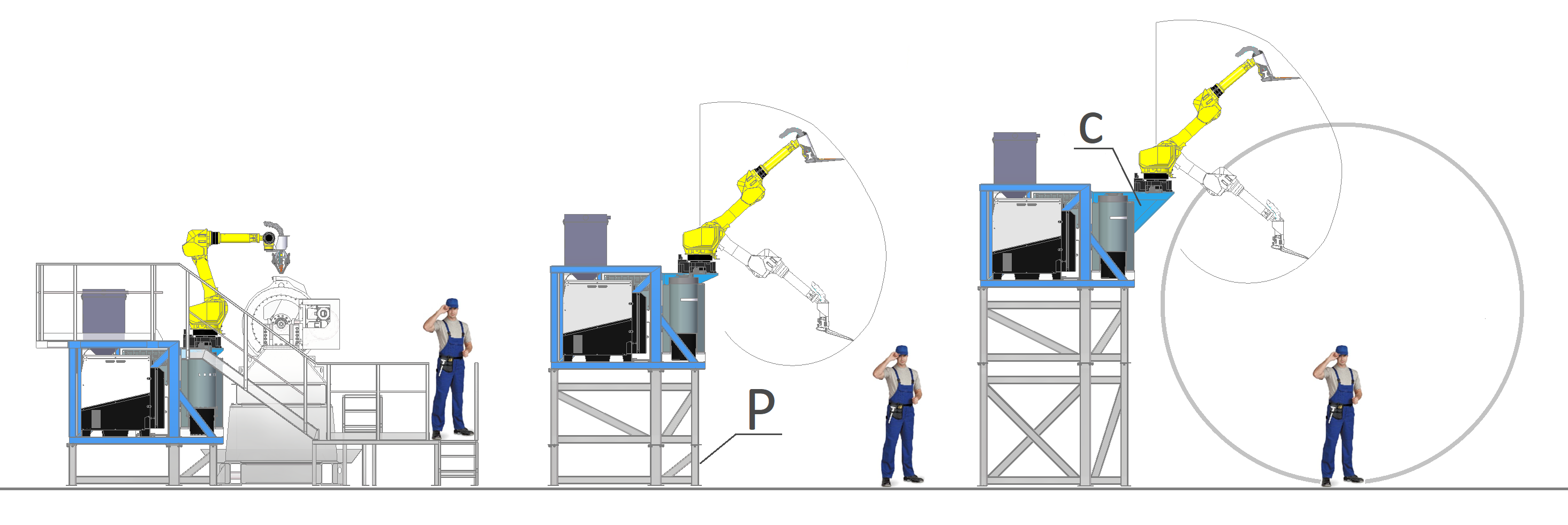
A robot and a welding machine from various manufacturers can be installed on the module.
A module manufactured at our facility dramatically reduces the costs of installation, repair, and commissioning work.
3. Operating system
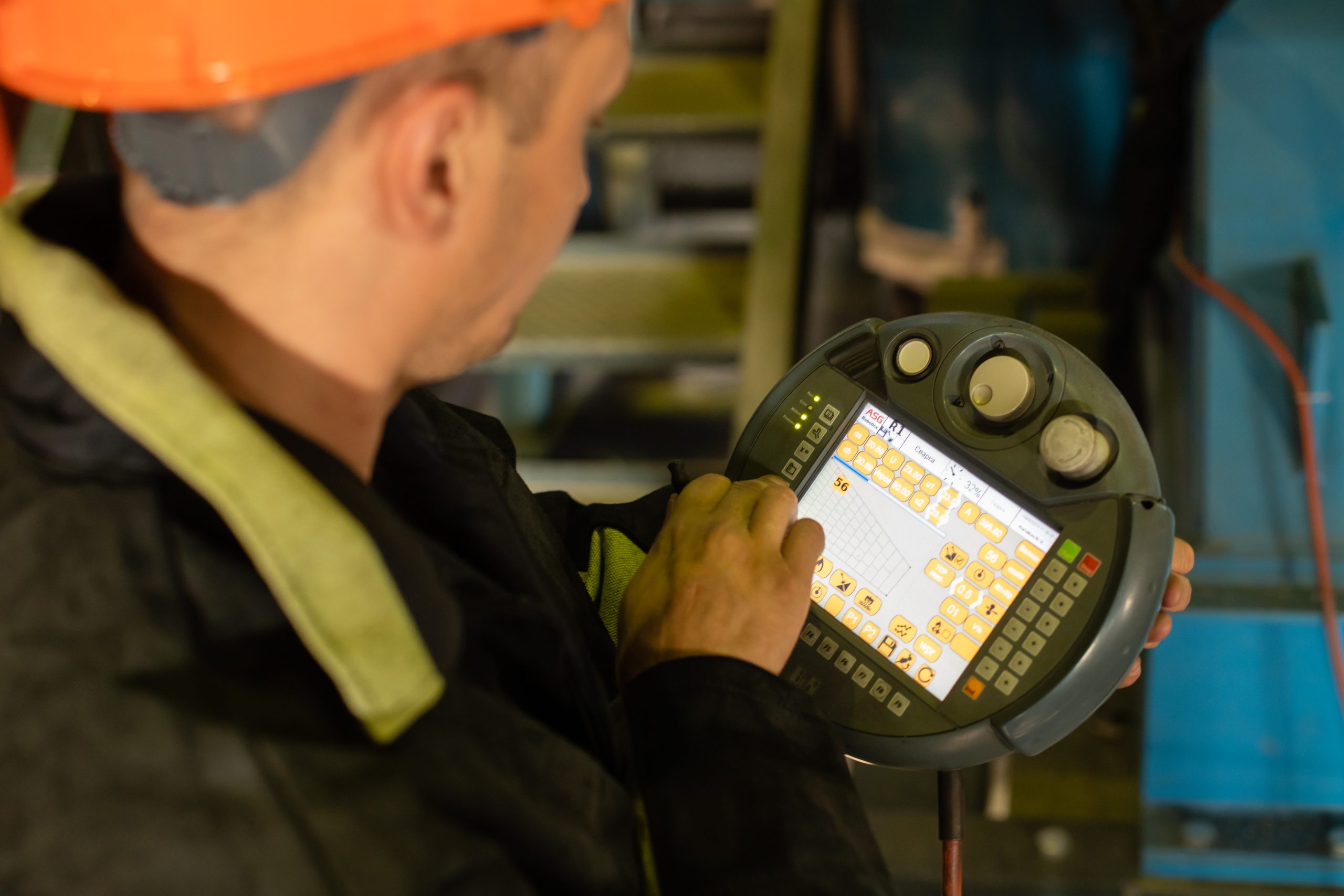
The high computing power of the robot controller allows it to control all devices, including the welding machine, welding head, flux recirculation system, laser tracking systems, cooling system and temperature control system near the heat-affected zone.
By creating robotic solutions, we have achieved significant improvements in welding quality and productivity.All this allows us to say with confidence that we can perform any welding work, circular or longitudinal seams of all types of connections.